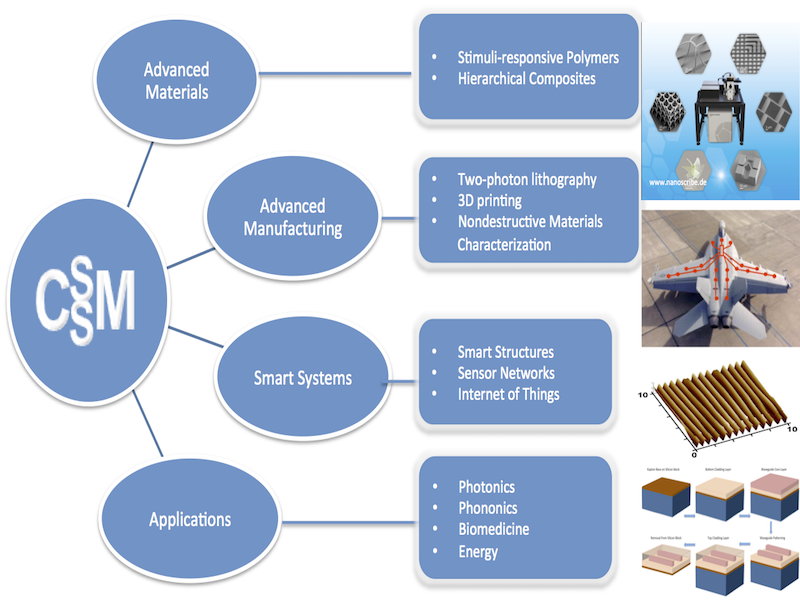
Multiscale Fabrication
Nature has successfully integrated multiphase components at multiple scales to create remarkable functional devices. The mammalian ear is an example of a nonlinear electro-chemo-mechanical device that integrates multiphase components at multiple scales. The result is a remarkable sensor with large dynamic range (through a possibly active nonlinear amplifier) and exceptional frequency discrimination (through frequency-selective wave localization). The fundamental premise of this research effort is that such multiscale multiphase integration is essential for engineered systems to exhibit functionality beyond what is currently achievable.
Two-photon 3D Printing
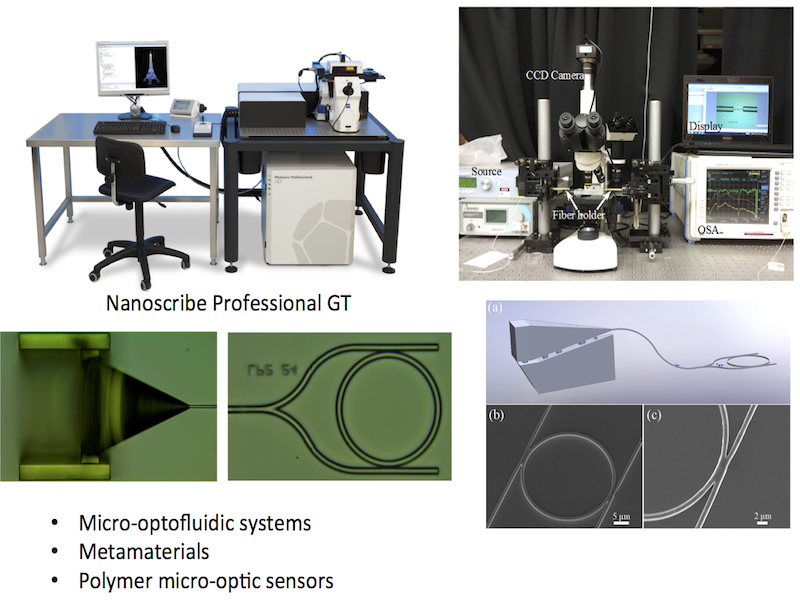
Two-photon lithography is useful for creating sub-micron scale 3D polymer structures. At CSSM, we have a commercial system from Nanoscribe that is used to create complex 3D structures in a wide range of projects in collaboration with several groups at NU and beyond. Applications include micro-optofluidic devices, metamaterials, and polymer micro-optic sensors.
Multi-Photon Direct Laser Writing
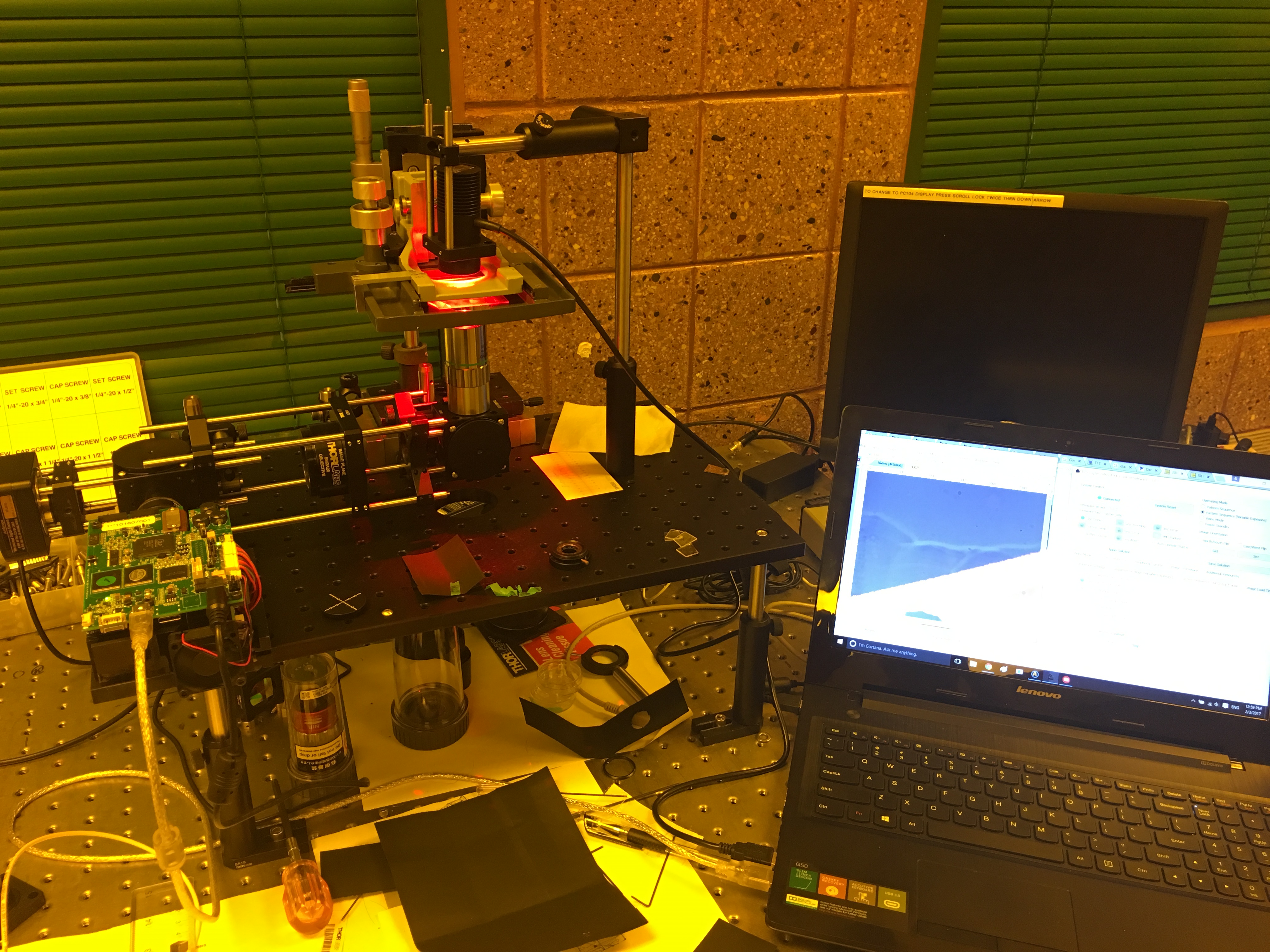
Assisted Surface Nanopatterning
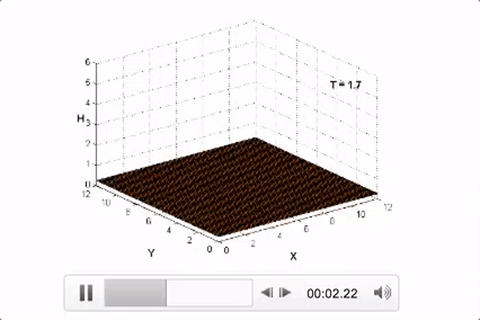
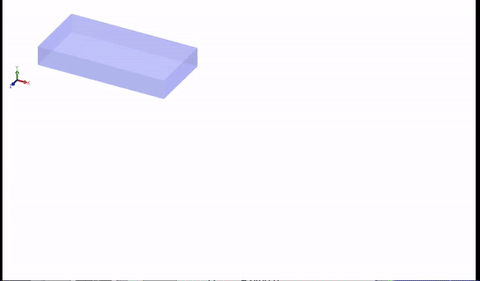
Laser-Assisted Blistering
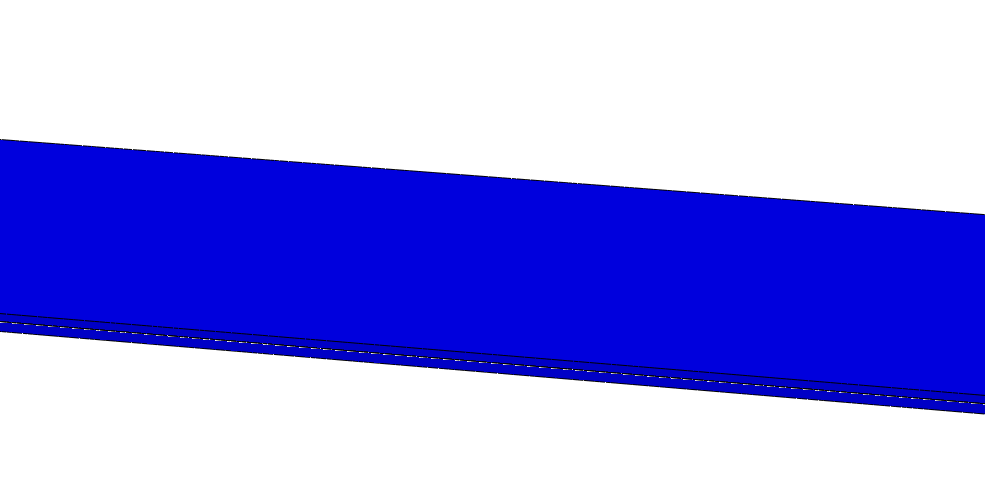
Smart Materials
We are developing stimuli-responsive polymeric materials for both 3D printing and 2D assisted surface patterning.
Stimuli-Responsive Polymers for 3D Microstructures
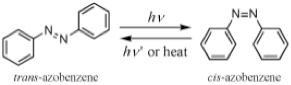
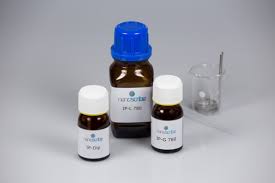
In this work, we are investigating several azobenzene-functionalized polymers to identify suitable resists for direct laser writing of 3D microstructures using two-photon polymerization. These resists must retain the azobenzene trans-cis transformation for subsequent single-photon optically triggered reconfigurability. Applications to reconfigurable 3D micro-optofluidic systems are being developed.
Optically Active Polymers
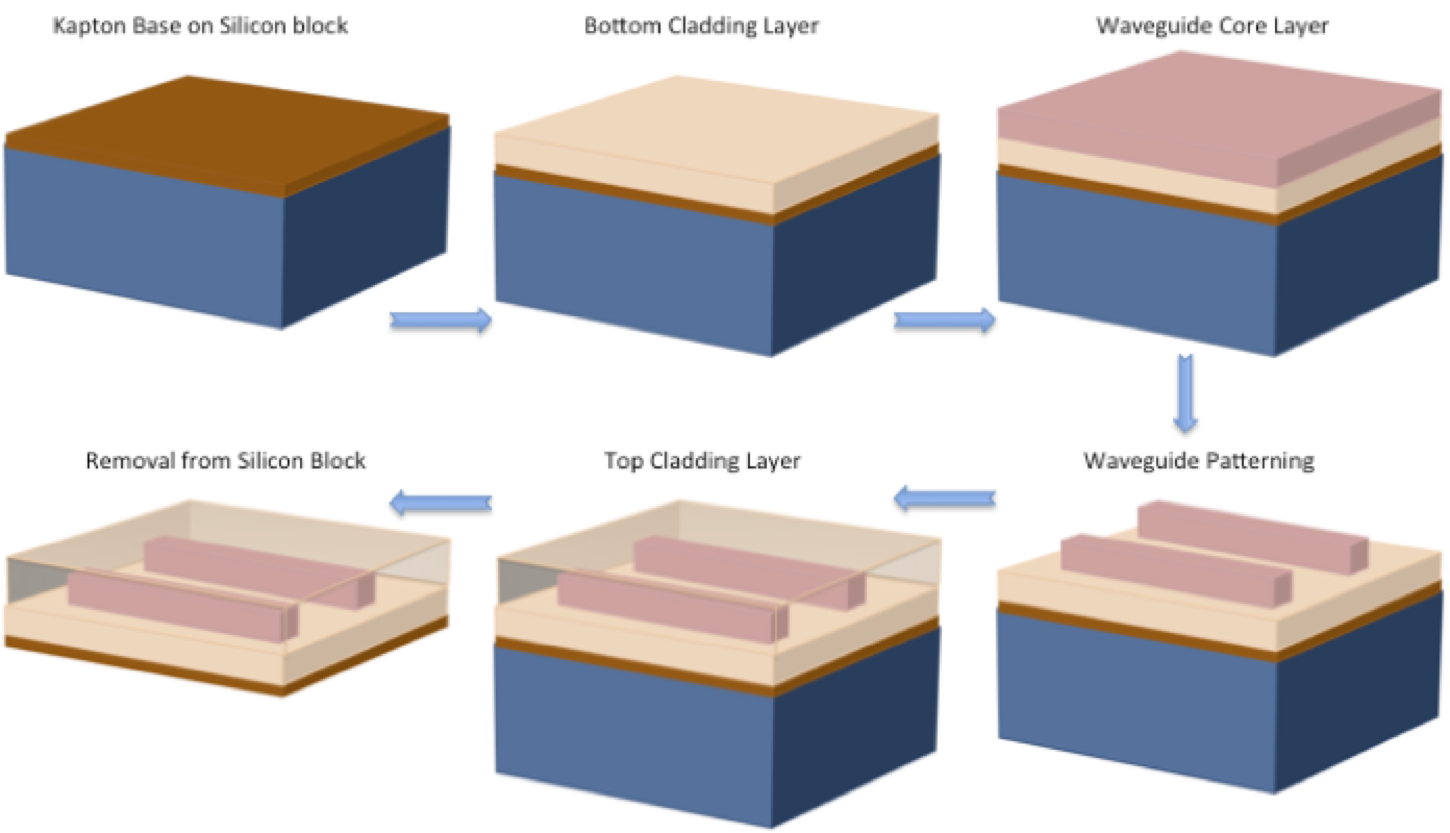
In this work, we are investigating several optically-active nanoparticles for integration into photoresists that enable fabrication of active micro-ring resonators and polymer optical amplifiers. Applications to sensing systems are being developed.
Metamaterials
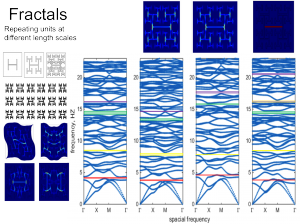
Metamaterials for photonic and phononic control are being investigated both theoretically and experimentally.
Shape Memory Polymers for Assisted Surface Nanopatterning
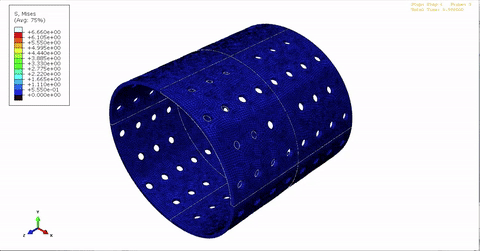
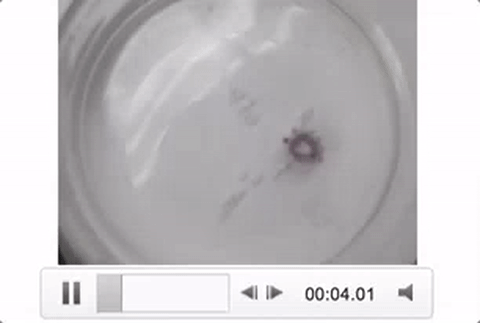
We have developed shape-memory polymers for use in the fabrication of complex 3D structures. We have also developed systems for assisted surface nano-patterning. Thermomechanical response of shape memory polymers has been modeled using a physics-based two-phase model that has been integrated into large-deformation finite-element codes.
Smart Structures
Smart Structures are structures that have integrated sensing capabilities, may offer unusual properties by virtue of their geometric or material design, or may offer the possibility of reconfigurability in response to external stimuli. We are developing fiber-optic and micro-optical sensors that can be intergrated into structures.
Mesoscale Integrated Optical Systems
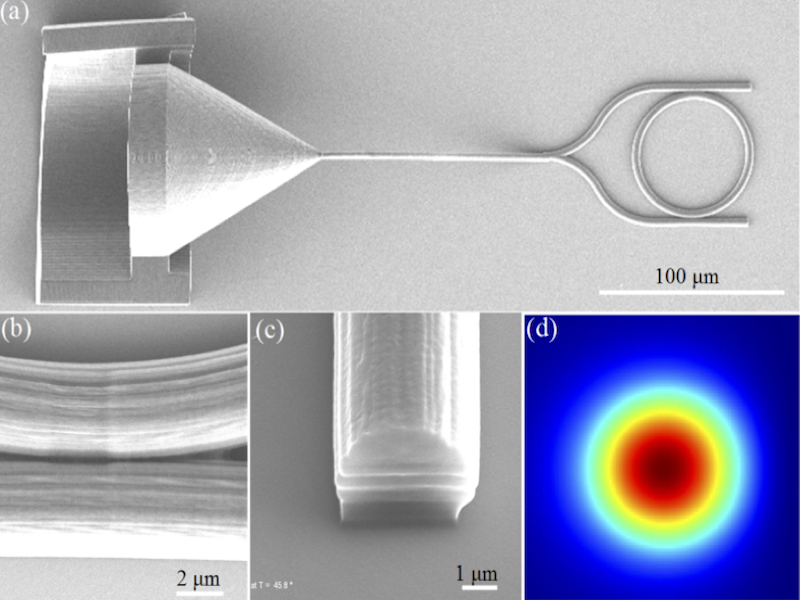
In this project, we are developing Mesoscale Integrated Photonic Systems (MIPS) aimed at making photonic sensor systems robust enough to be integrated into real structures. The sensors are fabricated using two-photon lithography. We are developing polymer waveguide-based rigid and flexible MIPS and demonstrating their utility as strain and chemical sensors.
Fiber-Optic Chemical Sensors

We are developing chemical sensors based on nanocoated photonic crystal fibers that exhibit enhanced sensitivity and selectivity.
Fiber-Optic Dynamic Strain Sensors
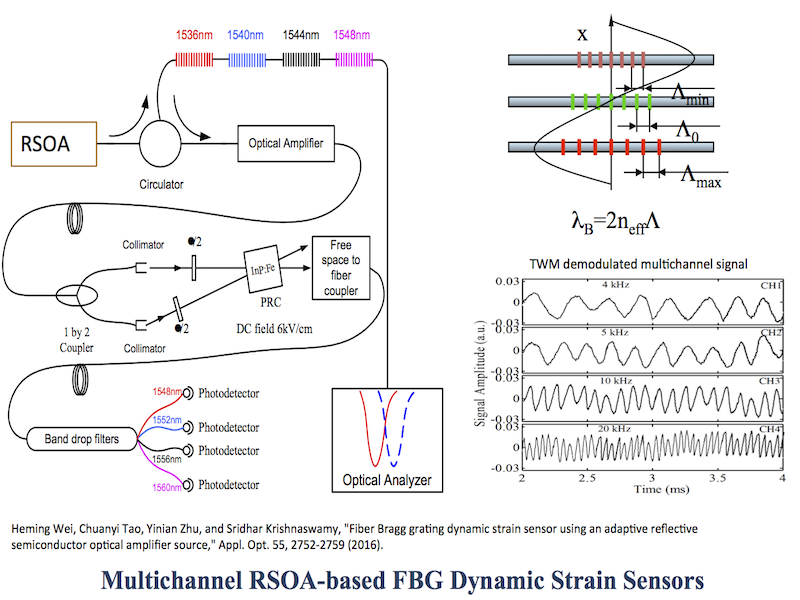
We are developing fiber-optic dynamic strain sensors that are adaptive to quasistatic drift. These systems integrate two-wave mixing spectral demodulators with adaptive-sources to provide multiplexed sensing for acoustic emission and impact detection.
Graphene-Based Thin Film Sensors
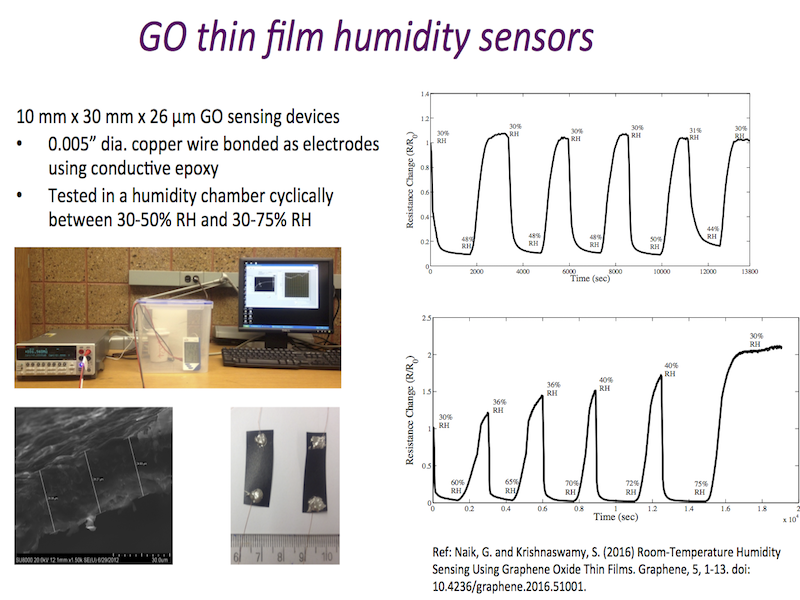
We have developed graphene-oxide thin film chemical sensors for humidity detection. We have also developed graphene-based strain sensors with gage factors that are 3 orders of magnitude higher than conventional foil strain gauges.
Materials Characterization
Photoacoustic techniques are a subset of ultrasonic methods wherein laser generated stress waves are used to obtain information about structural and material properties. In photoacoustic techniques, the ultrasound is typically also detected using non-contact optical detection, thereby enabling truly non-contact nondestructive characterization of the material properties of structures. Photoacoustic techniques have found application over length scales ranging from macro-structures to nanometer-sized thin films and coatings.
Picosecond Ultrasonics at the Nanoscale
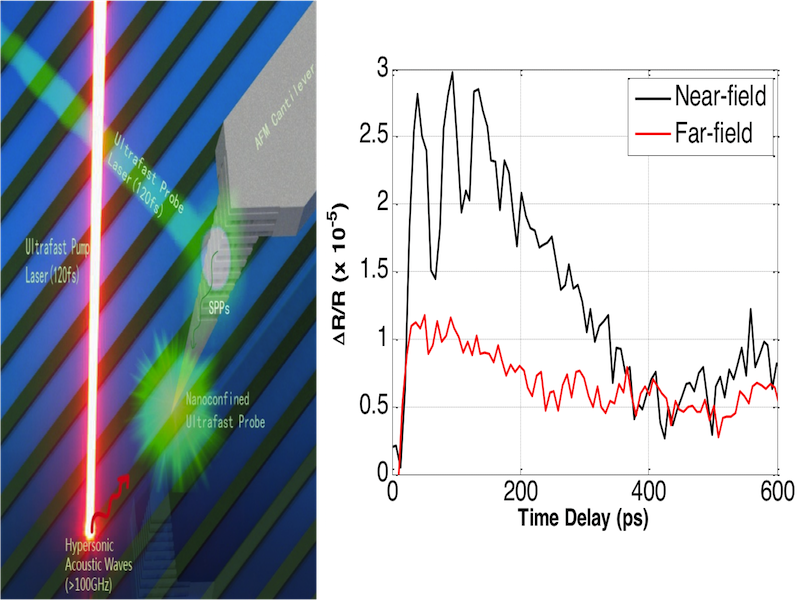
Laser-Ultrasonic Sensing of Additive Manufacturing Processes
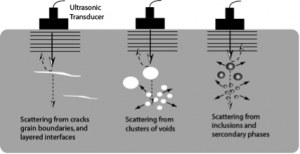
Photoacoustic Characterization of Thin Films
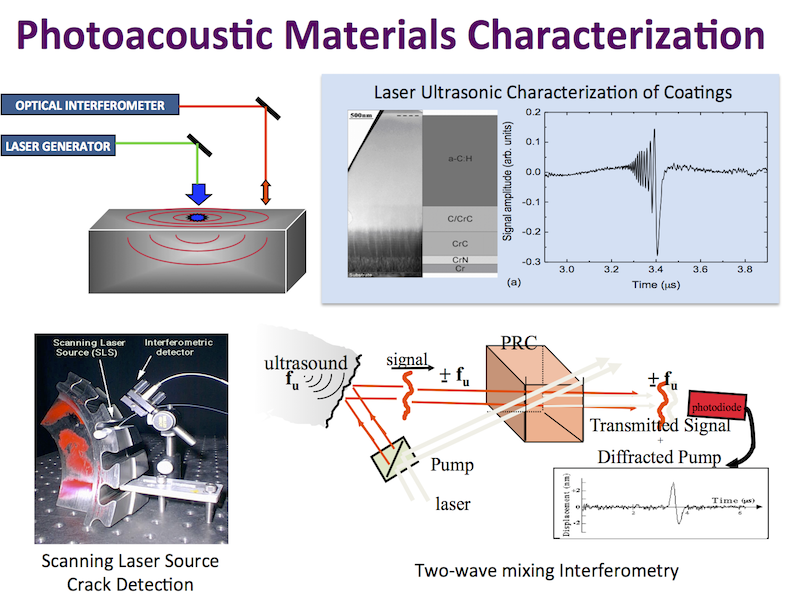
Photoacoustic Characterization of Defects
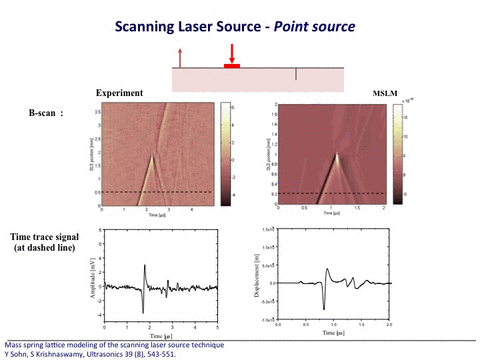
Photoacoustic methods can be used for ultrasonic defect imaging in structures such as turbine blades, GLARE composites, etc. The traditional mode of application of laser ultrasonics for defect imaging parallels conventional pitch-catch ultrasonic inspection mode, except that lasers are used to generate and detect the ultrasound. For detecting very small defects, the pitch-catch technique requires that the scatterrer reflect a significant fraction of the incident wave, and furthermore that the generating and receiving locations be in line and normal to the scatterrer. In our labs, we have developed a novel Scanning Laser Source (SLS) technique for detecting very small near surface scatterrers that are arbitrarily oriented with respect to the generating and detecting directions. The SLS technique has no counterpart in conventional ultrasonic inspection methodologies as it relies on near-field scattering and variations in thermoelastic generation of ultrasound in the presence and absence of defects. In the SLS technique, the ultrasound generation source, which is a point or a line-focused high-power laser beam, is swept across the test specimen surface and passes over surface-breaking flaws (see figure). The generated ultrasonic wave packet is detected using an optical interferometer or a conventional contact piezoelectric transducer either at a fixed location on the specimen or at a fixed distance between the source and receiver. The ultrasonic signal that arrives at the Rayleigh wave speed is monitored as the SLS is scanned. It can be seen that the amplitude and frequency of the measured ultrasonic signal have specific variations when the laser source approaches, passes over, and moves behind the defect.
Structural Health Monitoring
Intelligent Structural Health Management systems facilitate taking timely remedial actions in order to prevent catastrophic structural failure by incorporating diagnostic sensor data for closed-loop prognosis of remaining structural integrity. We are developing both diagnostics tools for SHM (described under Smart Structures) as well as probabilistic prognostic tools to assess the structural integrity of safety-critical structures.
Prognostics
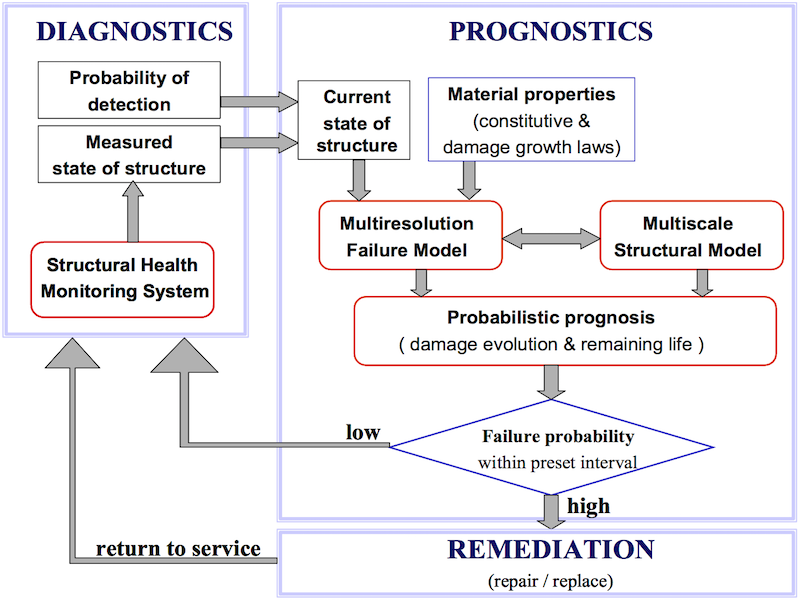
Research efforts in this area include probabilistic degradation models (SK & JDA), analytical modeling of scattering of ultrasonic waves by defects (JDA), and physics-based modeling of environmental degradation (JDA).